5G時代的到來,更多高頻高功率的設備也隨之涌現,伴隨著這些器件的產生,如何高效散熱成為一個亟待解決問題。對于熱管理材料而言,一定時間內傳導熱量的多少不僅取決于熱導率的高低,還與其厚度有關,這就類似于水管傳導水流,流速一定時,水管越粗,傳導的水量越多。所以,高效的熱管理材料,即具有高熱通量的材料,需要同時具備高熱導率和高厚度兩個要素。目前常用的熱管理材料主要可以分為金屬材料和非金屬材料。傳統的金屬材料由于其易加工性可以很容易做厚,但是其導熱依賴于其有限的自由電子數量,所以熱導率比較有限,銀是熱導率最高的金屬,熱導率也僅僅只有429 W m-1 K-1。而熱導率高的非金屬材料,主要是碳基膜,例如碳化的聚酰亞胺膜和高定向熱解石墨,卻很難做厚,所以制備高熱通量的導熱膜仍面臨挑戰。
石墨烯膜由于其優異的導電導熱性能而備受關注,目前微米級石墨烯膜的導熱率最高可以做到1940W m-1 K-1。就石墨烯厚膜的方法而言,其加工工藝可以分為兩大類,一是基于石墨烯和氧化石墨烯的溶液加工方式,另一種是基于石墨烯粉體的壓制工藝。前者由于溶劑的揮發不均勻性(表層溶劑揮發形成殼層結構限制了內層溶劑的揮發)等因素,制備出的石墨烯厚膜具有較低的取向度,導熱率不高;后者制得的膜由于粉體之間的邊界難以消除,往往具有較低的導熱率,所以尚未實現通過直接方法制備兼具高厚度和高導熱的石墨烯膜。為解決這一問題,浙江大學高超教授團隊提出一種基于氧化石墨烯自融合效應的間接粘接的方法來實現高熱通量石墨烯厚膜的制備。相關成果以“Ultrathick and highly thermally conductive graphene films by self-fusion strategy”為題發表在《Carbon》(doi: 10.1016/j.carbon.2020.05.051)上,論文第一作者為17級碩士生張曉東。
研究亮點
1. 利用納米膜的粘接證明了氧化石墨烯膜在粘接以及石墨化后,可以實現晶格融合,即原子尺度的融合。
2. 利用氧化石墨烯的自融合效應,通過粘接不同層數的氧化石墨烯膜,經過干燥、熱壓、石墨化、冷壓之后,得到了不同厚度且無界面層離的石墨烯膜。
3. 證明了隨厚度的變化,該方法制備的石墨烯膜的導熱率和導電率變化比較穩定,最厚的24層石墨烯膜(厚度約為200 μm)仍然保持有1220 W m-1 K-1的熱導率和6.91×105 S m-1的電導率。
4. 證明了制備的石墨烯厚膜具有高熱通量。在文中展示的傳熱模型中24層石墨烯膜的熱通量為0.2002 J s-1, 兩倍于具有相同厚度的銅箔(熱通量為0.0955 J s-1),也明顯高于具有較小厚度的石墨烯膜。
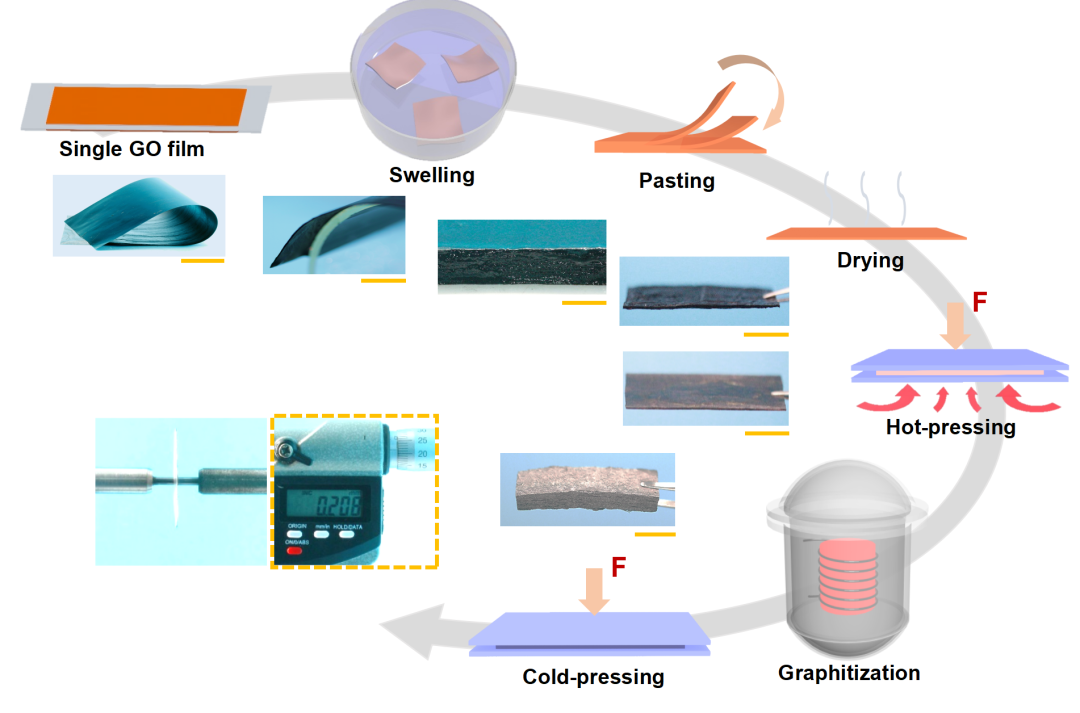
圖1: 石墨烯厚膜的制備流程。標尺自上而下分別是:4cm,1cm,1cm,1cm,1cm,1cm。
石墨烯厚膜的制備分為溶脹、粘接、干燥、熱壓、石墨化、冷壓等幾個步驟(圖1)。其中溶脹的作用是使GO膜表面的含氧官能團活化,以便在粘接過程中形成氫鍵,使相鄰的膜之間實現界面融合。采用熱壓法進行預還原可以防止在300 ℃以下快速逸出的氣體破壞組裝膜的完整性。石墨化并經300 MPa的冷壓后即得到了200 μm厚的石墨烯厚膜,其密度在2.0?2.1 g / cm3之間。
圖2 :(a)單張GO膜截面。(b-d)粘接、熱壓、及石墨化后的3層膜的截面。(e-h)粘接法制備的6層、12層、16層、和24層石墨烯膜。
在電鏡下觀察粘接法制備的三層GO膜的截面可以發現(圖2b),其與單層GO膜的截面只有厚度的差異,而無結構的不同。且經熱壓(圖2c)和石墨化(圖2d)后,均沒有層離結構出現,整個截面呈現出均一完整的結構。即使將粘接層數提高到6層、12層、16層和24層,所得石墨烯膜都沒出現層離結構,且具有致密且高取向的結構。
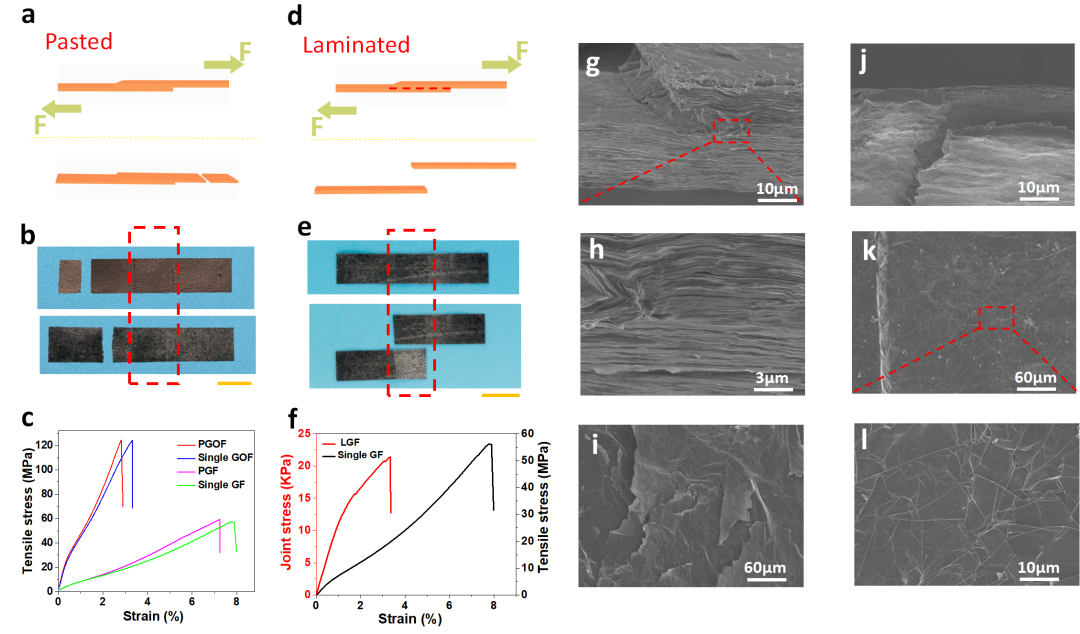
圖3:(a-f)錯位粘接的GO膜(PGOF),錯位粘接的石墨烯膜(PGF)和錯位層壓的石墨烯膜(LGF)的搭接剪切測量。(a,d)搭接剪切測量示意圖。(b)拉伸破壞后PGOF(上)和PGF(下)的照片。標尺:5mm。(c)PGF和PGOF的剪切應力-應變曲線。(e)斷裂前后的LGF照片。標尺:5mm。(f)LGF的連接應力-應變曲線。(g,h)PGOF的截面圖。(i)PGF連接表面。(j)LGF的截面。(k,l)LGF連接表面。
應用搭接-剪切測量表征粘接界面的連接強度。錯位粘接的GO膜呈現出與單張GO膜相當的拉伸強度(122 MPa),經過石墨化后依然保持單張石墨烯膜相似的力學性能,進一步確認了兩張膜的緊密連接(圖3c)。與之相反的是,錯位層壓的兩張石墨烯膜的連接強度極低,只有21.4 KPa(圖3f)。SEM下也可以很清楚地看出,粘接法消除了兩張膜之間的界面(圖3g和h)。當將兩張膜沿界面撕開時,分離的表面布滿碎片(圖3i)。這些證據證明粘接法可以實現兩張膜的充分融合。
圖4:(a)納米膜之間融合的機理。(b)TEM下30 nm石墨烯膜的截面。(c,d)TEM下粘接法制備的60 nm石墨烯膜截面。
進一步地,將兩張30 nm厚的GO膜進行粘接并石墨化,觀察其在TEM下截面的晶格結構。可以看出,粘接膜呈現出和單張膜相同的完美晶格結構,且在粘接界面處,晶格依然連續,表明兩張膜在粘接并石墨化后實現了原子尺度的融合(圖4c和d)。
圖5:(a-c)SEM下PGF,BGF和LGF的截面。(d)PGF和BGF的XRD圖譜。(e)三種膜的熱導率與厚度的關系。(f)三種膜的電導率與厚度的關系。
作為對照,亦通過層壓法(LGF)和直接刮涂法(BGF)制備了與粘接法(PGF)相同層數(或厚度)的石墨烯膜。可以看出相比于LGF的層離結構(圖5b)和BGF的低取向結構(圖5c),PGF具有致密且高取向的結構(圖5a)。這種結構賦予了其優異的導熱導電性能,其導熱率和導電率基本不隨厚度的升高而降低,厚度達到200 μm以上時其仍然保持有1224 W m-1 K-1的熱導率和6.91×105 S m-1的電導率。而BGF由于隨著刮涂厚度的增加膜的取向度降低導致其導熱率在35 μm處驟減,隨后漸漸趨于穩定。LGF的導熱率隨層數的增加一直有下降的趨勢,24層LGF的導熱率為646 W m?1 K?1,只有PGF的一半。
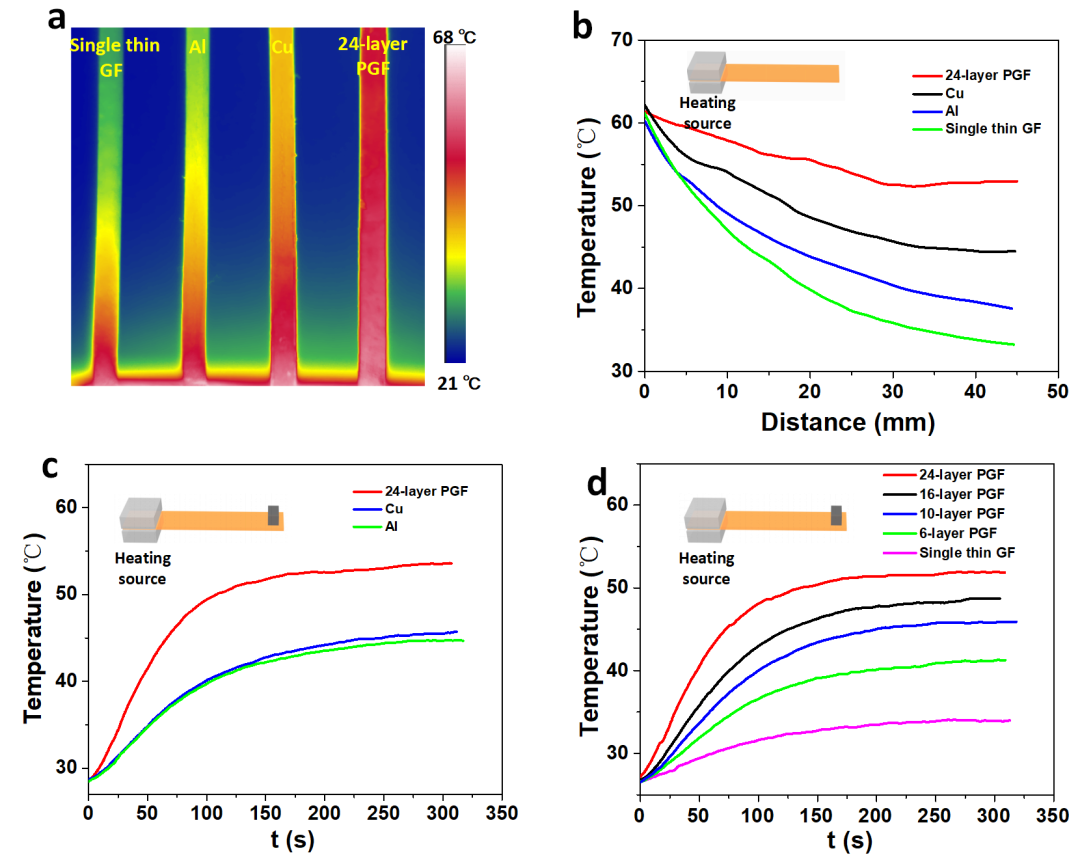
圖6:(a)200 μm的PGF,Cu箔和Al箔以及10 μm的石墨烯膜的紅外熱像圖。(b)根據紅外熱像圖所繪的各膜溫度分布曲線。(c)應用不同種類膜加熱石墨塊(5mm×5mm×20mm)的溫度與時間的關系。所有的膜尺寸為40mm×20mm×0.2mm。(d)應用不同厚度的石墨烯膜加熱石墨塊時的溫度與時間的關系。
紅外熱圖像直觀地比較了200 μm的PGF,Cu箔和Al箔以及10 μm的石墨烯膜的傳熱速度,不難看出同時具有高厚度和高熱導率的PGF展現出了最快的傳熱速度,整張膜的溫度分布最均勻(圖6a和b)。用恒溫熱源(68℃)分別通過以上膜加熱石墨塊(圖6c),發現應用PGF加熱石墨塊的溫度上升最快,平衡溫度最高。對前25s時各膜的熱通量進行粗略的計算,PGF的平均熱通量為0.2002 J s-1,是銅箔(0.0955 J s-1)的兩倍。而且24層PGF的傳熱速度也要明顯高于較小層數的PGF。表明高熱通量取決于高厚度和高導熱率兩個因素。
該方法為制備高熱通量熱管理材料提供了一種新的思路,也拓寬了石墨烯膜作為導熱材料的應用可能。該論文得到了國家自然科學基金、國家重點研發項目、浙江省重點研發計劃和浙江大學百人計劃等相關經費的資助。
原文鏈接:https://doi.org/10.1016/j.carbon.2020.05.051
- 南京大學張煒銘/潘丙才課題組在氧化石墨烯膜限域分離策略及其水處理應用方面取得新進展 2020-09-15
- 浙江大學高超教授團隊實現環境穩定高導電石墨烯膜 2019-10-16
- 北航趙勇教授、王女副教授課題組:仿生溫度響應石墨烯膜用于門控及分子分離 2017-12-15